Implementing Lean waste management at Trivium factory
This case illustrates a comprehensive approach to waste management, emphasizing the potential for significant improvements in sustainability and operational efficiency within the manufacturing sector.
Mil-teks optimisations in Trivium factory brought forth numerous advantages
In an ambitious endeavor to combat the issue of waste production, Trivium Packaging sought the expertise of Mil-tek. Our waste optimisation on the factory significantly streamlined waste disposal, reducing the volume of waste by a ratio of 10:1 and consequently lowering the frequency of external waste collection. Moreover, internal transport of waste by truck was reduced by 60%.
0%
Set a goal of “Zero waste to landfill”
Trivium Packaging is a multinational entity renowned for its recyclable metal containers used across various industries. In order to address the problem of overproduction of packaging waste, the company decided to improve waste management procedures and reduce landfill contribution at one of its factories in England.
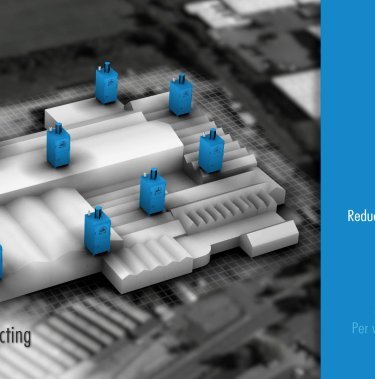
Challenges encountered at the factory
Initially, the factory’s waste management involved accumulating waste throughout the premises, followed by frequent transportation to external dumpsters via trucks. This routine not only increased the risk of on-site accidents due to the heavy internal truck traffic but also cluttered the production area with waste awaiting disposal. This created an untidy and inefficient working environment.
Additionally, the constant need to manage waste distracted workers from their primary responsibilities, adversely affecting the production line’s efficiency and the factory’s overall productivity.
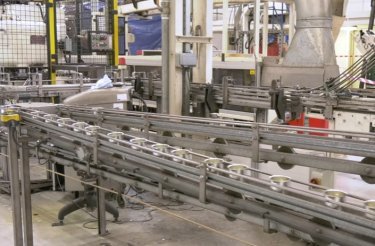
Mil-tek’s analysis and proposed solutions
Mil-tek’s intervention began with a detailed value stream mapping, identifying that the existing Lean manufacturing approach at the factory failed to extend its benefits to waste management.
It was found that workers wasted considerable time and effort transporting waste externally. Actually, it was revealed that each worker had to walk 300 meters across forklift paths more than ten times per shift to dispose of waste externally.
Recognizing the inefficiency, Mil-tek suggested that eliminating this waste management step was crucial. In order to maximize operational efficiency, we recommended integrating waste compactors straight into the production line, in keeping with the 5S methodology.
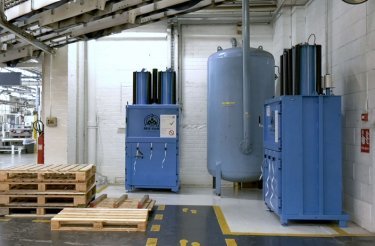
Implementing pneumatic balers on production line
Mil-tek’s solution involved installing pneumatic balers directly within the production area, utilizing existing air lines to ensure optimal efficiency.
This allowed workers to dispose of waste immediately on-site without the need for external transportation.
Thanks to the balers’ ability to compact waste by a ratio of 10:1, the frequency of external waste collection trips saw a dramatic decrease.
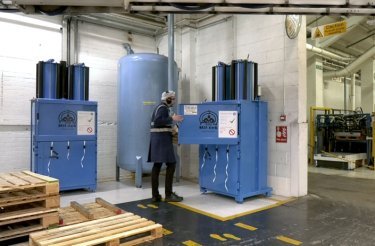
Broader impacts of the waste reduction initiative
Following the initial success, Mil-tek’s balers have been introduced in additional factory areas, aiding Trivium in its mission to minimize landfill waste and progress towards a zero-waste goal.
Mil-tek’s waste optimisation on the Trivium factory not only facilitated a cleaner, more efficient production line but also brought forth numerous advantages, such as:
- financial savings
- enhanced productivity
- a reduced environmental impact
- a safer working environment
- ultimately contributing to Trivium’s goal towards achieving zero waste to landfill
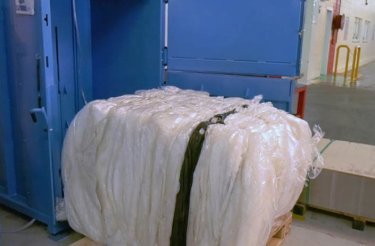
Have a question?
You are always welcome to contact us with any kinds of questions.
We can help your business save time, space and money!